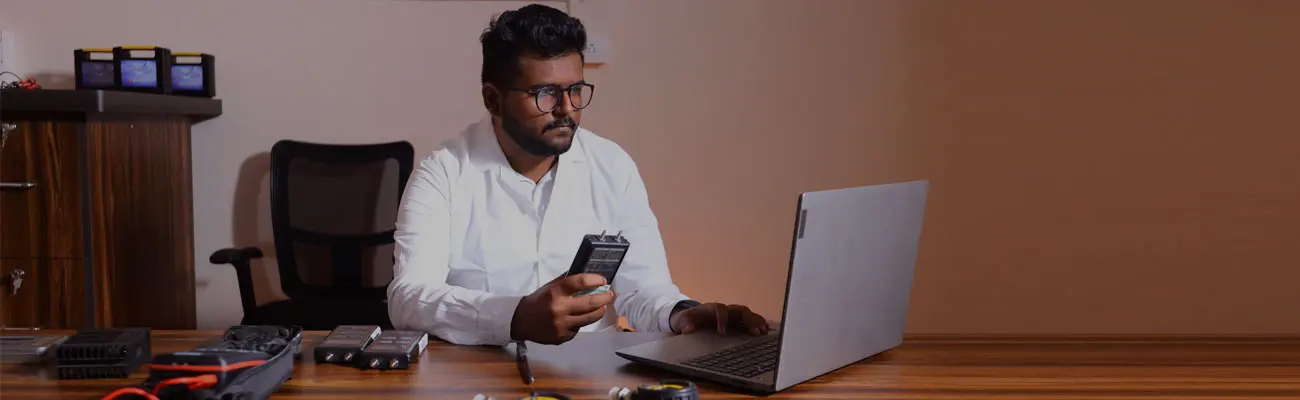
What exactly is calibration?
Formally, calibration is a documented comparison of a calibrated measurement device against a traceable reference standard/device. The reference standard may also be referred to as a “Master / Calibrator.” Technically, the master standard should have higher accuracy than the device to be calibrated.
Calibration is a comparison between a known measurement (the standard) and the test instrument.
One talks about verification when the calibration is carried out or supervised by an official body. Therefore, the quality of the displayed values is determined by both of these variants. No intervention to the measuring instrument itself is allowed. With the adjustment, it is understood that there is an intervention to the measuring device to minimize a detected measuring deviation. Typically, adjustment is followed by further calibration to check and document the final state of the measuring instrument following the intervention.
In contrast to verification, which will lose its validity after a while set by law, the calibration validity period is subject to functional specifications such as manufacturer’s instructions, requirements of a quality assurance standard, or in-house and customer-specific regulations. Calibration must also be carried out to measure the instrument manufacturer products subject to official supervision, such as drugs or foodstuffs.
How often do we have to calibrate?
You can calibrate once a year. It also depends on the usage of devices.
Now, what are the general terms in calibration?
- Accuracy: Accuracy is precision with calibration. Precision, however, does not ensure accuracy.
- Resolution / Least Count: The smallest value measured by an instrument is called the least count. Resolution is the smallest increment a tool can detect and display
- Deviation: Difference between standard reading and test reading
- Uncertainty: Measurement uncertainty is critical to risk assessment and decision-making. Organizations make decisions every day based on reports containing quantitative measurement data.
- Calibration Certificate: Calibration certificates are required for all test and measurement equipment to control critical test functions or acquire test data.
PRESSURE:
How are pressure gauges calibrated?
To calibrate a pressure gauge, we need to source the pressure applied to the gauge. It is more common to use a pressure calibration hand pump to generate pressure and an accurate pressure measurement device (calibrator) to measure the pressure.
Why does a differential pressure transmitter need calibration?
This equipment will sense the difference in pressure between two ports and produce an output signal regarding a calibrated pressure range. In the Differential pressure transmitter, flow is directly proportional to Differential pressure.
Calibration of Differential Pressure Switch:
The differential pressure switch is one of the most widely used instruments in the BMS industry. It is used to sense the difference between two pressure sources with a switch to On/Off, which acts as a relay / Alarm. This switch plays a vital role. So calibration of the Pressure switch is very important.
TEMPERATURE:
The temperature sensor plays a vital role in the accuracy of the whole temperature measurement loop. The temperature sensor needs regular calibration to have accuracy with any measurement instrument.
Do RTDs need to be calibrated?
There is no adjustment to an RTD after it is built, so any calibration checks the resistance at a given temperature. Measures determined that a better standard was required for temperature, and the International Practical Temperature Scale was born.
To calibrate a temperature sensor with any sensing element, one requires a temperature bath as a source to generate temperature and a reference Sensor of a similar sensing element to compare the values. Output can be measured as desired, like either temperature in degree C / Voltage / mA.
Temperature Transmitter:
The performance of temperature transmitters and related instruments can decline, especially in the harsh environments found in industrial settings. Temperature transmitter calibration maintains reliability and uptime. A temperature transmitter comprises a sensor and a transmitter which both affect the final output displayed.
HUMIDITY:
Most calibration laboratory equipment and processes are to some degree sensitive to ambient temperature and relative humidity. Calibration uncertainties depend on maintaining temperature and relative humidity within certain tolerances. Deviations outside of limits can cause large uncertainties and disqualify calibration work.
The humidity generator selected for the calibration system had sufficient accuracy as the relative humidity standard. However, its inherent temperature accuracy was inadequate for this application. A separate temperature reference would need to transmit the temperature readings to the computer through a digital interface.
Calibrating one or two temperature/relative humidity sensors in an environmental chamber is common practice. In this case, the large number of sensors that needed calibration and the required low uncertainties were uncommon.
The chamber is the most significant factor that complicated the development of this calibration system. Special efforts are put into the design of the calibration system, achievement of low uncertainties, address these and other issues.
Calibration is a must because:
- Over time, sensors are deteriorating through different exposures to environmental effects such as vibrations and extreme temperatures.
- The possible drift is due to the long period of continuous usage while exposed to different factors in the environment.
- Increases production yields
- Optimizes resources
- Assures consistency
- It is fundamental to compliance with international, regulatory, or industry-sector-specific standards that require measurements to be ‘traceable to national standards and, in doing so,
- Ensures measurements (and perhaps products) are compatible with those made elsewhere.
As a result, it is a very wise decision to calibrate the instruments regularly.
CALIBRATION CERTIFICATE:
When calibration is performed, the certificate or report is the end product and represents the only tangible evidence of the service that the purchaser can link to the expenditure. Its importance is obvious for that reason alone. Not only does it show the results obtained across the scope of testing, but it is also a key means of judging the quality of the calibration provider’s service.
Most calibration laboratories offer several forms of a certificate, but the apparent similarity in their names can be confusing. Before placing an order, understand what exactly the offer is to ensure it meets our needs.
Calibration is simply the process of comparing with a known standard and reporting the results.
For example: Applied = 1.30V, Indicated = 1.26V (or Error = -0.04V)
Calibration may include adjustments to correct any deviation from the value of the standard.
As it relates to calibration, verification involves evaluating these results against a specification, usually the manufacturer’s published performance figures for the product.
No calibration is perfect. There is always some degree of uncertainty about the ‘true value of a measurement. Contributors to this ‘potential for inaccuracy’ include the performance of the equipment used to make the measurement, the test process itself, and environmental effects.
Measuring the behaviour of the item results in additional imprecision. A Technical person will assess and combine these various contributions in an uncertain budget.